Health
A Guide to High-Precision Silicone Parts
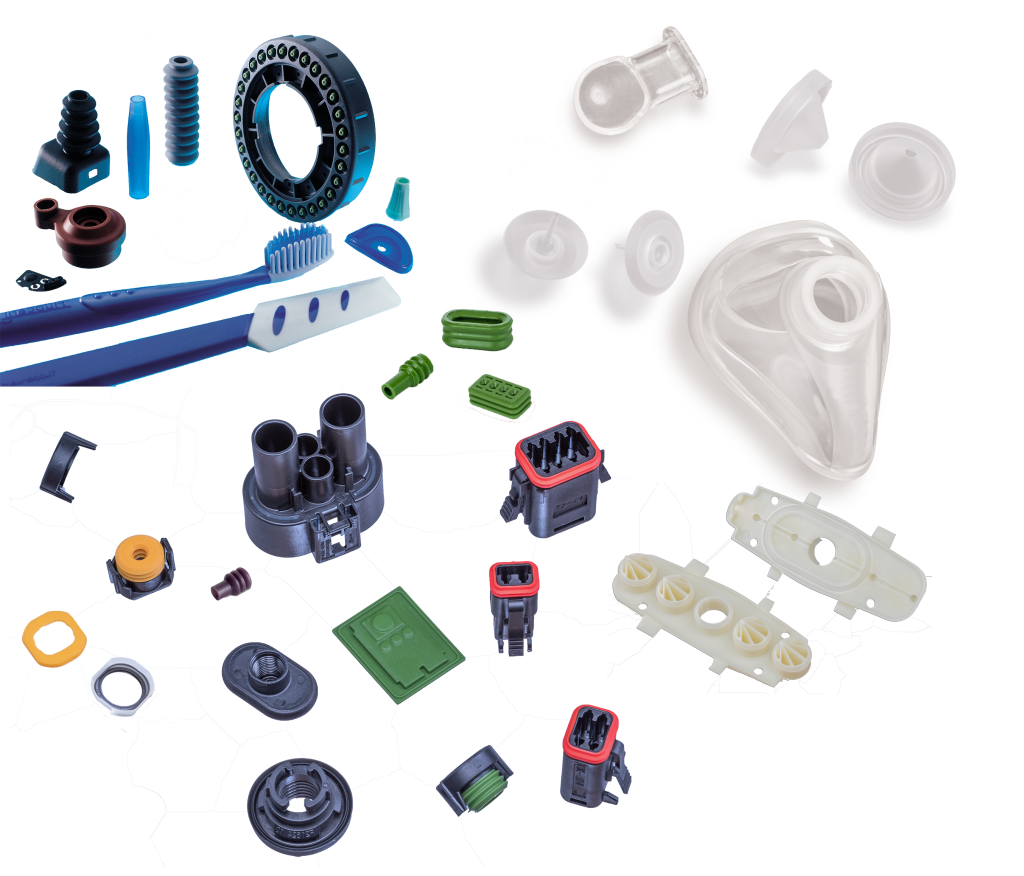
Liquid Silicone Rubber (LSR) injection molding is a quickly rising manufacturing approach for creating high-quality, intricate silicone components. This versatile course of gives quite a few benefits over conventional strategies, making it a useful instrument for a variety of industries. This complete information delves into the world of LSR injection molding, explaining its core ideas, purposes, and the advantages it gives.
Understanding Liquid Silicone Rubber (LSR)
LSR, also called Liquid Silicone Elastomer, is a kind of silicone rubber that exists in a liquid state earlier than present process a curing course of. This distinctive attribute makes it ideally suited for injection molding, permitting for exact shaping and mass manufacturing. LSR boasts a exceptional mixture of properties, together with:
- Biocompatibility: Protected for contact with human pores and skin and tissue, making it appropriate for medical units and child merchandise.
- Sturdiness: Presents glorious resistance to UV rays, ozone, and excessive temperatures.
- Flexibility: Maintains its elasticity inside a large temperature vary.
- Chemical Resistance: Inert to many chemical compounds and oils.
- Excessive Tear Energy: Resists ripping and tearing.
- Dimensional Stability: Retains its form nicely after molding.
The LSR Injection Molding Course of: A Step-by-Step Breakdown
LSR injection molding includes meticulously managed steps to make sure constant, high-quality half manufacturing. Right here’s a breakdown of the important thing phases:
- Mildew Design and Manufacturing: An important first step is designing a mildew that exactly replicates the specified half geometry. LSR molds are usually crafted from metal or aluminum to resist the strain and warmth concerned within the course of.
- Materials Preparation: LSR is available in two separate components: base (A-side) and catalyst (B-side). These parts are saved in devoted containers and maintained at managed temperatures for optimum processing.
- Metering and Mixing: Throughout injection, exact metering pumps precisely measure the required quantities of A and B parts. These parts are then blended completely throughout the machine’s mixing unit to provoke the curing response.
- Injection and Mildew Clamping: The blended LSR is injected into the closed mildew cavity below excessive strain. The mildew stays clamped shut to make sure the LSR fills all cavities and maintains its form throughout curing.
- Curing: Warmth and strain are utilized throughout the mildew to speed up the LSR’s curing course of. Curing instances can differ relying on the half thickness and complexity.
- Half Ejection and Ending: As soon as cured, the mildew opens, and the completed silicone half is ejected. Relying on the applying, components could bear further processes like trimming or floor therapies.
Benefits of LSR Injection Molding
LSR injection molding gives a large number of advantages in comparison with different silicone half manufacturing methods:
- Excessive Precision and Repeatability: The managed injection course of permits for constant half dimensions and complicated element replication.
- Mass Manufacturing: LSR injection molding is well-suited for high-volume manufacturing runs, making certain environment friendly and cost-effective manufacturing.
- Minimal Flashing: The managed nature of injection molding minimizes extra materials (flash) formation, decreasing ending necessities.
- Automation Potential: The method is very automatable, resulting in elevated manufacturing effectivity and decreased labor prices.
- Huge Materials Choice: A various vary of LSR formulations can be found to cater to particular utility necessities, similar to various hardness, coloration, and flame retardancy.
- Quick Cycle Occasions: In comparison with conventional strategies, lsr injection molding gives quicker cycle instances, resulting in faster manufacturing turnaround.
Purposes of LSR Injection Molded Components
The flexibility of LSR and the precision of the injection molding course of make it a useful instrument throughout quite a few industries. Listed here are some distinguished purposes of LSR injection molded components:
- Medical Units: Elements like valves, seals, gaskets, and tubing for medical devices and tools.
- Client Electronics: Keypads, buttons, seals, and protecting parts for digital units.
- Automotive: Gaskets, seals, and vibration dampeners for varied automotive purposes.
- Child Merchandise: Nipples, teethers, and different gentle parts for child bottles and toys.
- Family Home equipment: Seals, gaskets, and vibration dampeners in home equipment like dishwashers and washing machines.
- Meals and Beverage: Seals, gaskets, and valves for meals processing tools.
Conclusion: LSR Injection Molding – A Pioneering Manufacturing Method
LSR injection molding has revolutionized the manufacturing of high-precision silicone components. Its distinctive mixture of fabric properties, course of management, and flexibility makes it a pretty choice for a variety of industries. As know-how continues to advance, LSR injection molding is poised to play a fair higher position in shaping the way forward for silicone half manufacturing.